Cold chain packaging—how Medline got sustainable right
Medline’s 100% recyclable temperature-controlled packaging leads the way
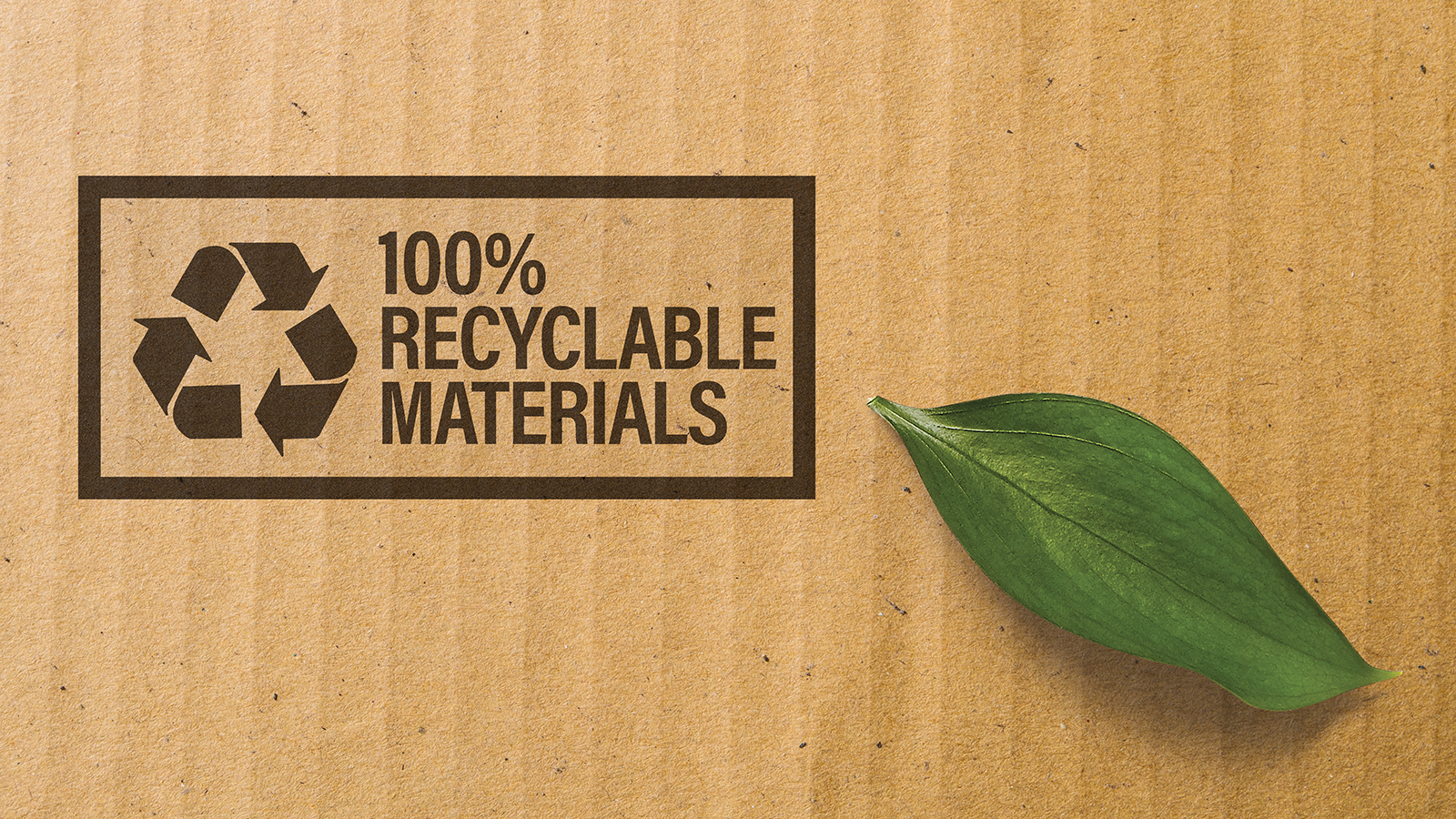
In 2020, Medline introduced a major innovation—100% recyclable cold chain supply packaging. Among the first major medical distributors to get it right, Medline’s breakthrough began simply—by listening to complaints.
“Many of our lab company customers were unhappy with the amount of Styrofoam, plastic and packaging going into cold chain packaging industry-wide,” says Jim Burgess, Medline Director of Sustainability. “We also heard that packaging wasn’t protective enough, things were getting damaged in delivery. We listened.”
Perfect timing for an out-of-the-box response
A cross-functional Medline team had just been formed to tackle packaging issues—engineers and experts in R&D, sustainability, operations and design. Looking for its first project, the Sustainable Packaging Lab now had it.
Less than a year later, Medline was delivering cold chain healthcare products to lab customers across the country in a whole new way. Vaccines, lab refrigerated items, COVID-19 and other tests, plated and tubed culture media—all transported in perfectly controlled, sustainable ecosystems. But designing sustainable packaging that could maintain temperatures between 2 and 8 degrees Celsius (35 and 46 degrees Fahrenheit) was a challenging journey.
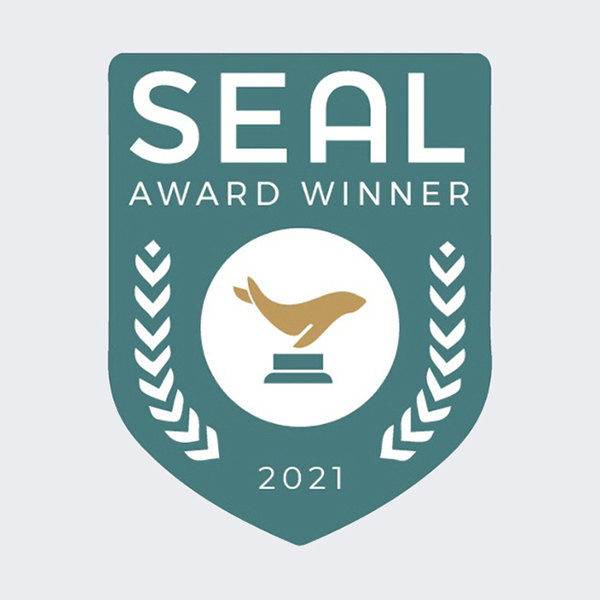
Medline’s cold chain packaging and other solutions received the 2021 Sustainability, Environmental Achievement and Leadership (SEAL) Business Sustainability Award in the category of Environmental Initiatives.
The biogel brick and other breakthroughs
“We knew customers wanted something sustainable, recyclable and easy to break down, but getting all of that, plus proper cold storage, in one solution was tricky,” says Travis Smith, Medline Director of Lab Product Operations.
“What really set us apart was finding and sourcing a biogel brick that keeps things cold. It’s a corn-based gel that can be safely poured down the drain. The plastic is recycled. Gel bricks others use all have some level of toxicity and go to landfill.”
Efficiency on the line
Standardizing temperature-controlled packing across different box sizes was another challenge. Keeping things cold to tight 2-8 degree Celsius specifications involves brick size, brick placement in the box, and packing materials that protect the product.
“For efficiency and quality control on the lines, we wanted the same packing procedure for all five of our box sizes,” says Smith. “You can take Box A and pack it out one way, but box B, C, D and E? Each one is a different story, but we found a way to pack out consistently.”
Fast Facts
Since cold chain packaging’s go live in April, 2022, Medline has:
- Operated 99,357 cold chain lines
- Packed 73,263 100% recyclable boxes
- Shipped 26,665 COVID home test kits for the federal government
- Sold 100K+ HbA1c Reagent Kits
The full package comes together
Things were falling in place. Thin liners made from recycled materials replaced bulky styrofoam liners. The cooling brick’s plastic gel casing could be fully recycled. The gel was drain-safe. Thinner chipboard pallet sheets made it possible to load trucks more densely—and were made from 54 percent post-consumer recycled content.
Using cutting-edge sensors and thermocouples, the team tested interior packaging temperatures in special chambers replicating conditions the packages would encounter during distribution.
Soon, a fully tested, market ready solution was complete, now assembled and used in Medline’s 11 cold chain distribution branches across the US.
A story of cold chain savings
“There’s a belief that sustainable products are more expensive,” says Burgess, “but the new packaging can help healthcare facilities save money. Fewer cutaways and restocks help reduce personnel costs. Delivery capacity is expanded. Their landfill and waste management costs drop.”
“When we used pre-built Styrofoam coolers we could fit about 300 boxes on a truck. It was like shipping air,” Smith says. “Now materials ship to us flat and densely packed and we fit about 1,500-2,000 boxes per truck, assembling them ourselves. That’s efficient.”
“There’s a belief that sustainable products are more expensive, but the new packaging helps healthcare facilities save money.”
Jim Burgess
Medline Director of Sustainability
100% recyclable packaging
Earlier cold chain packaging underutilized space and generated unnecessary waste. The Sustainable Packaging Lab scrapped previous delivery, shipping and storage methods and introduced a sustainable and efficient solution in less than a year.
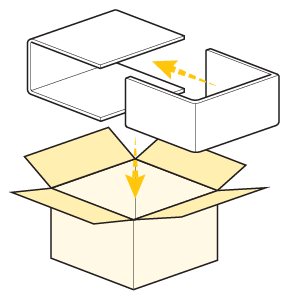
Thinner chipboard pallet sheets
Facility storage methods determine how much product can be housed per branch—which impacts ability to deliver on time. The new chipboard pallet sheets enable material cost savings and better warehouse utilization.
- Made from 54% post-consumer recycled content
- Saves 46,000 lbs. of paper
- Optimizes storage space
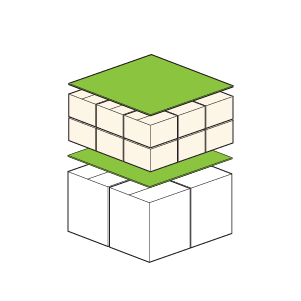
A cost-effective, easy recycling stream
When customers need to dispose of packaging, everything can be put it into the same recycling stream. No separating of materials is required. That’s another advantage.
Says Burgess, “Recycling keeps trash out of big dumpsters and in some states, even offsets a company’s trash output, lowering or even eliminating a garbage disposal bill.”
Customers want sustainable packaging
People believe that investing in sustainability is the right thing to do, but it’s the right thing for business, too – allowing less packaging, more efficient shipping and less damage to product.
“Sustainability matters to people,” says Burgess. “We’re listening to that and changing business practices to better serve our customers and the environment.”