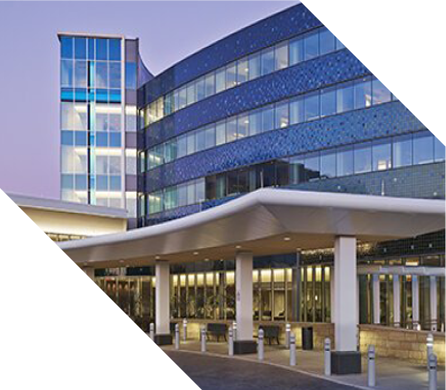
Insight
The age-old saying “collaboration is key” is thrown about as often as you see a discussion about the value of partnership. But how often does that collaboration result in $2 million of savings? In Medline’s first-ever clinical standardization summit, the goal was lofty: bring together different regional and clinical expertise to conduct product sampling and discuss opportunities for supply chain standardization. Still, no one could have expected how successful the collaboration would be.
One of the key insights drawn from the experience was this: the infection prevention team, on the clinical side, is integral to a provider’s supply chain. In meeting organizational goals and evaluating products for efficacy and safety, they serve an invaluable role in ensuring the right products are chosen, so as to reduce waste and unnecessary supply spending. By involving clinicians early on, they have a voice in the process, which leads to improved patient outcomes and reduced variability in care.
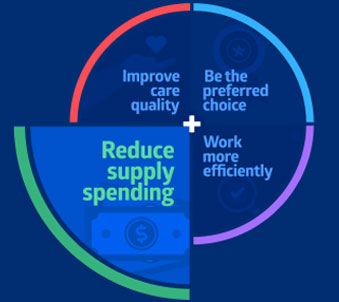
Organization
Bon Secours Mercy Health (BSMH)
One of the top 20 health systems in the United States, BSMH is part of the top performing quartile of Catholic health systems for lowest cost per case for patient care. This care is provided by more than 57,000 employees serving communities throughout Florida, Kentucky, Maryland, New York, Ohio, South Carolina and Virginia.
Challenges
- Employ standardization across 12 product categories
- Reduce SKUs by 44 percent
- Reduce manufacturers from 250 to 48
Actions
BSMH had identified 21 categories ideal for standardization. Using an RFP process, they narrowed down to a few vendors, thereby able to make immediate decisions during the summit on systemwide standardizations.
Results
Reduce supply spending:
In just one week, Cincinnati, Ohio-based Bon Secours Mercy Health was able to uncover an immediate $2.1 million savings in its supply chain.
Challenges
The summit, structured as a collaborative, in-person workshop, was a new Medline program for healthcare providers and supply chain teams. Teams consisted of experts spanning clinical, infection prevention and supply chain specialties—many of whom never had met in person, despite working together remotely for years. The groups collaborated to drive the following initiatives:
• Employ standardization across 12 product categories
• Reduce SKUs by 44 percent
• Reduce manufacturers from 250 to 48
“Standardization is vital for direct patient caregivers because we want to do the same thing every time we do a particular task or procedure,” explains Anne Macy, system director for infection prevention, Bon Secours Mercy Health. “That provides reliability for the patient and improves our patient outcomes overall.”
Ultimately, there are many challenges to overcome when uniting the supply chains of two companies—Bon Secours and Mercy Health, which had recently merged. According to Whitaker, one of the biggest issues to address was the different enterprise resource planning (ERP) systems. Data analytics is often quite labor intensive, especially when companies are coming in from different places. Also, having an interdisciplinary team or approach is not always the standard and can require a shift in culture and attitudes to bring everyone together. Collaboration is crucial when evaluating analytics and making data-driven decisions that will ultimately save in time, money and resources.
There were also the challenges associated with prioritizing patient outcomes over cost. BSMH, like many providers, sometimes select products that are more expensive because they are thought to provide better patient outcomes. Ultimately, savings can often come through the reality of reduced infections and reduced readmissions, which are more costly and have a deeper negative impact on operations. The goal is to find the balance, and product standardization is often the key.
“By taking the best of the best between the two groups, the outcome is far superior to what we’ve had independently, which further strengthens our desire to improve care and outcomes.”
Amy Whitaker
RN, BSN and Vice President of Supply Chain Clinical Integration, Bon Secours Mercy Health
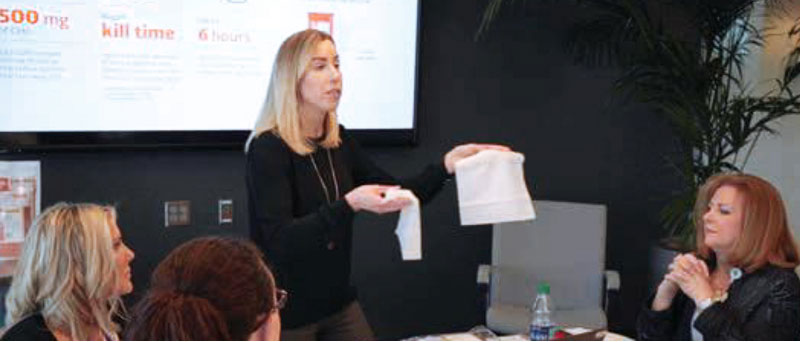
Actions
The first step in the summit was to break wound care and infection prevention representatives into separate groups. Thirteen wound care clinicians from the system met in the first half of the week, and the 13 infection prevention clinicians met later in the week. Each team reviewed samples of products, category by category and evaluated each individually, so the clinicians could decide which ones they liked best. Kyle Hoffmann, market director at Medline, stated, “The hands-on approach and access to both Medline clinical and product teams provided the summit with great momentum.”
During each clinical breakout session at the summit, BSMH’s supply chain team was in attendance, along with Medline. Together, they provided a great deal of analysis and documentation so that decisions could be made immediately. Product designers, product managers, clinical teams and quality assurance teams who presented on the categories and products being evaluated were also in attendance. All of this collaboration allowed for an open forum where teams could ask questions about development, get feedback and see firsthand the outcomes of the clinical programs behind the solutions.
And in the end, attendees approved two areas of clinical focus and expertise for the entire healthcare system:
1. Skin Health Solution: Empowers frontline staff to consistently and confidently care for at risk with best practice guidance, staff education and a system of products.
2. Infection Prevention: Through Medline’s 3-zone defense strategy program, the health system will work with Medline to design kits that help guide bedside nurses in using the correct prevention process every time.
“This collaboration elevates what it means to be an integrated partner. Teams are eager to build on these supply chain decisions and see how reducing practice variation through intuitive design and evidence-based practice can improve outcomes.”
Kyle Hoffman
Market Director, Medline
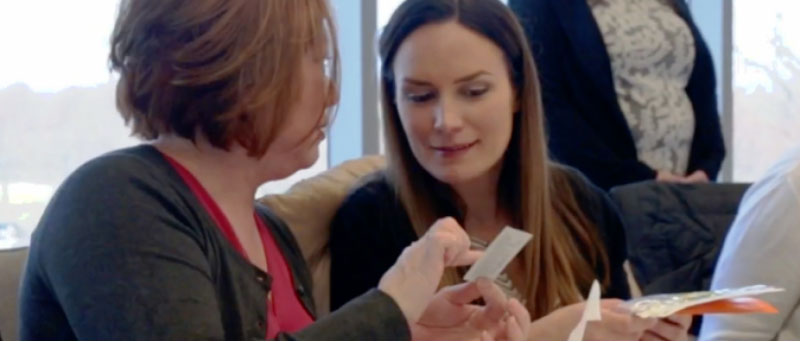
Results
The one-week meeting looked to reduce supply spending and drive improvements in quality and patient safety throughout the newly formed health system, after the merger of Bon Secours with Mercy Health. When Medline organized the event at its headquarters in Northfield, Illinois, the goal was direct: let’s find standardization through our vendor and product selection and find key ways to reduce supply spending as a result. The summit resulted in $2 million in savings for the organization in the way of reducing overlap and unnecessary products.
$2.1M
Savings in reduced overlap and unnecessary purchases
44%
SKU reduction after the merger of Bon Secours and Mercy Health
Some additional and important standardizations that came out of the meeting, included:
- Central line dressing standardization
- Hand hygiene product standardization
- Cleaning product standardization
- Urologic product line standardization
- Chlorohexidine skin prep product standardization
- Oral care kit standardization
The meeting was also the first time many of the team members met in person. As Hoffman says, “Standardization is so important for health systems. Calls and meetings work, but take longer, so getting all stakeholders in one room is very beneficial.”
References:
- https://newsroom.medline.com/infection-prevention/infectious-diseases-like-coronavirus-prep
- Strong supply chain bolsters patient care. Internal NorthShore newsletter.