Supply Chain Efficiencies Help Caregivers Stay Focused
How to spend less time on tasks and more time on patients.
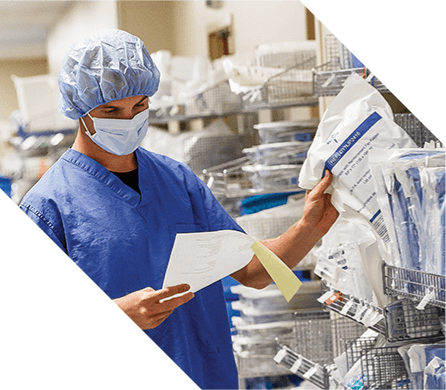
Insight
We see it every day—nurses spending valuable time hunting down items, putting away supplies or filling out paperwork. In fact, studies show that nurses may spend less than two hours of a 12-hour shift on direct patient care.1 We know that when clinicians are able to spend more time caring for patients, people are less likely to fall, suffer from infections or worse. Mix-ups with medication or treatment also decrease with nurses on hand, and patients report being more satisfied with their care.
With rising pressure to improve quality, safety and performance, health systems need to embrace new processes that are easy to implement and follow. The plan is to create efficiencies that help caregivers stay focused on what they do best: provide patient care. And here’s the thing, process improvement for supply chain logistics doesn’t always mean having to adopt a high-tech approach, as you will see in this case study. When it comes to saving time, the goal is simple: to reduce nonclinical tasks so that clinicians can spend more time with patients. It’s not about more time in a day; it’s about less time spent doing things that can be better managed through the supply chain. With that in mind, we worked with a leading regional health system to streamline their supply management in two significant ways.
Organization
Leading health system in southern Indiana and Kentucky
Headquartered in Kentucky, this family of hospitals, care centers, physician offices and health facilities is the largest not-for-profit health system in the state. They own or manage nine hospitals totaling more than 2,700 licensed beds and have more than 300 points of care—including outpatient facilities, which offer urgent care, express care, occupational medicine, physical therapy and diagnostics. Home care is also available in 39 Kentucky counties, six counties in Illinois and six counties in Southern Indiana. A physician network of more than 3,000 employed and affiliated physicians continues to grow as they endeavor to improve access to healthcare and enhance the health of Kentucky as a whole.
Challenges
- Replace automated point-of-use system with a more cost-effective solution
- Improve par optimization
- Enhance supply chain efficiency to reduce non-clinical tasks for staff
Actions
- Implement 2-bin inventory replenishment program for all supply rooms
- Employ enhanced LUM system: totes arrive “put-away-ready” in the supply rooms
Results
2-bin and enhanced LUM
- Confidently maintain accurate par levels in supply rooms
- Avoid costly upgrade
- Totes arrive “put-away-ready,” saving a minimum of one hour a day of labor
Challenges
Our partner was in the process of centralizing their supply chain activities, specifically their inventory systems and delivery methods. Their focus was on reducing costs, improving par optimization and enhancing overall efficiency. The system’s largest hospital, with 519 beds, had been using automated point-of-use cabinets to store and replenish supplies in the nursing floor par location areas for more than 20 years. Their current technological platform was approaching end of life within the next few years and required a substantial upgrade that would be costly and time consuming.
Less than 2 hours
Studies show that nurses may spend less than two
hours of a 12-hour shift on direct patient care.1
Actions
Excellence on par
As our partner was looking for cost-effective, efficient ways to manage supplies in par location areas, we collaborated with them, planning for a 2-bin inventory replenishment program for nursing floor par location areas at their Louisville hospital. Based on lean Kanban methods, the 2-bin system allowed for the use of the existing point-of-use-cabinets with only some minor retrofitting. By simply removing the cabinet doors, the hospital avoided the cost of redesigning all of their par location areas.
Enhanced inventory
For several years, the system has been utilizing LUM logistics for specific par location departmental delivery at several of their main hospitals. A major challenge was taking the extra step to transfer the totes from the pallet to a separate cart, which was then delivered to the specific departments. We worked with the group to implement an enhanced LUM Put-Away-Ready program. Now they no longer had to put the totes on the cart, rather, that step is completed at our nearby distribution center.
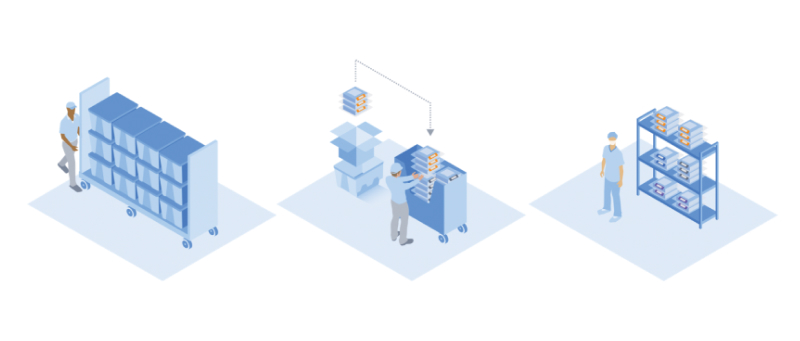
How it all works
Inventory management
The 2-bin inventory replenishment program allows for maintaining accurate par levels of products in well-organized bins, eliminating the traditional par item counting process. Here’s how it works:
Based on historical usage, predetermined quantities of each item are placed in two separate bins on a shelf—one bin is placed in the front and the other behind it. When the front bin is depleted, the nurse puts it in a designated area for the materials management staff to pick up. The back bin is then pulled forward on the shelf to be utilized by the staff. That empty bin is the trigger for replenishment. Our materials management staff restocks the bin and places it back on the shelf behind the first bin—achieving automatic, stock rotation. It’s a very simplistic, low-tech system, but very efficient for clinical staff and materials management.
If our par levels are set correctly, products will never expire, and stockouts are greatly minimized. This system also eliminates the tedious task of par counting. The key to success is establishing accurate par levels before implementation. We worked with Baptist to analyze and establish par levels, and a four-day par was implemented— two days for the front bin and two days for the back bin.
Each product has two assigned bins and each bin has three labels.
- One is a bar code for the materials management team that tells the inventory replenishment system which product and how many go in the bin. This part of the process is a huge time saver compared to the previous system.
- The second is a clinical, staff-friendly item description that is placed on the front of the bin for easy identification by clinical customers.
- The third sticker is a color-coded dot to easily identify the bin by product category, so respiratory products go together, wound care products are together, and so on.
Innovation doesn’t have to mean something new
A 2-bin par model was implemented in the system’s largest hospital—a significant improvement over the previous system for achieving replenishment, par level optimization and cost efficiency. Ultimately, 2-bin required no additional technology than the existing PeopleSoft ERP.
Similarly, a relatively simple enhancement was made to their LUM logistics service—improving efficiency and time management. This enhancement was the LUM “Put-Away-Ready” program, which eliminates the time-consuming step of staff putting the totes on the carts, freeing up their time for more important tasks.
“The improvements we’ve made in inventory management over the past couple of years have been remarkable. Chief among them are the enhancements to customer service to our physicians and other clinicians that ensure they have the right supplies, in the right place, at the right time and at the right price.”
Chief financial officer
Enhanced LUM
Our Put-Away-Ready program enables products to arrive at the hospital’s dock in lowest-unit-of-measure totes, on carts ready for delivery and ready to be put on a shelf for immediate use. When we’re loading totes on the cart at our nearby distribution center, we put a sort code on each tote that corresponds to a specific department. Generally, each cart contains bins for two or three departments that are geographically located near each other for the most efficient delivery. As our MedTrans trucks arrive at the docks, the products arrive in LUM totes, and on carts, pre-sorted based on the team’s put-away path, and ready for delivery to the departments to be stocked on the shelves. This improved process saves our partner at least one “man hour” a day, because it eliminates the need for staff to pull the totes off the pallets, re-sort them and then put them on carts to take up to the floors.
Results
As mentioned earlier, process improvement for supply chain logistics doesn’t always mean having to adopt a new or expensive technology system. Often, it takes evaluating an existing program and enhancing it for better efficiency all around. The advantages of the new system are clear: nurses no longer have to key in an ID number to open the cabinet, and they no longer have to count and record how many products they removed from the bin. They can now walk into a par location, grab what they need and get back to caring for patients. To date, more than 50 locations within the larger healthcare system have been converted to the new 2-bin inventory system, with about 15 more to go. They are also rolling it out at other hospitals on a piloted basis. Clinicians are comfortable using the process and, most importantly, have a high level of trust that they can get the products they need quickly and easily. For the materials management team, this system has saved so much time that our partner has been able to reallocate some team members’ time to work on other tasks. As for our Put-Away-Ready program, it ensures that supplies arrive unpacked, pre-organized and ready to use. Plus, items are delivered in just the right quantities needed for that day, freeing storage space for clinical use. The result: customers who are using this service have seen a 50% decrease in time spent on supplies.2
References:
- Collins, R. Bring Nurses Back to the Bedside. For the Record. 2015;27(9):10. Available at: https://www.fortherecordmag.com/archives/0915p10.shtml . Accessed January 6, 2021.
- Data on file
Please complete the form to receive additional content when published.
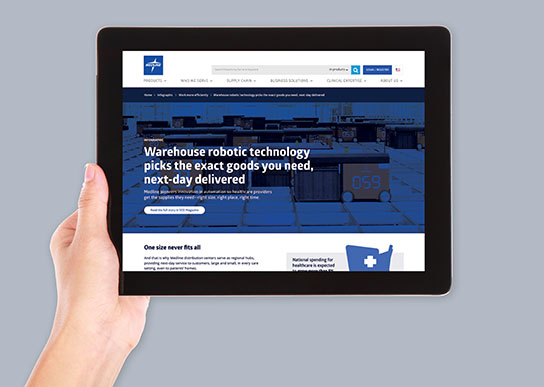
References
- Learn more about abaqis here.
- Discover more ways we’re helping providers make healthcare run better.
- See abaqis in action.
How can we help your business run better?
Contact us to learn more