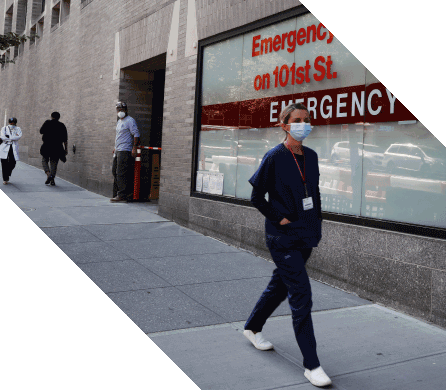
Insight
To many of us it felt more than surreal. How often do entire cities literally close down within a matter of days? In late February, early March 2020, the first signs of this were happening in the Pacific Northwest. Most of the country, however, with the exception of some key municipal leaders in cities on the coasts and even some in the Midwest, were not ready for what was about to hit. The rest, as they say, is history, with New York City suddenly becoming the epicenter of a raging pandemic that would eventually claim (and continues to claim) over half a million lives domestically within the coming year.
This case study chronicles the quick steps taken by Medline and the City of New York to not only find the appropriate space to house the inventory of PPE and other supplies the city had procured from the start of the pandemic, but to bring all this previously purchased inventory into Medline’s system and online platform. The inventory had to be accessible to and ordered by, as well as delivered on time to the municipal organizations—more than 1300 of them—that desperately needed them.
These operations were vast: first was the challenge of managing the physical stockpile itself (gathering all the supplies from various warehouses, storage spaces, freight and shipping ports throughout the city and get everything to one distribution center). That, ultimately, was the easy part. The bigger question loomed for Medline: “How do we provide visibility to the city—giving them and the various organizations coordinating care across the city access to the inventory through a robust ordering and delivery system?” Medline’s experience with supply chain optimization and third party logistics allowed them the flexibility to pivot and come up with a solution to manage all aspects of the project:
- Racking an empty warehouse in record time
- Materials and inventory itself
- Customer base and account creation
- Technology adaptations in SAP
- Bringing everything into Medline’s e-commerce platform
- Distribution to more than 1300 customers throughout the city
In the end, there were nearly 1300 unique organizations, from New York University to Mount Sinai Health System, from public schools to FDNY and NYPD, from small emergency operations to funeral homes—all these places needed access to supplies, and somebody had to coordinate all the orders and deliveries of the stockpiled inventory.
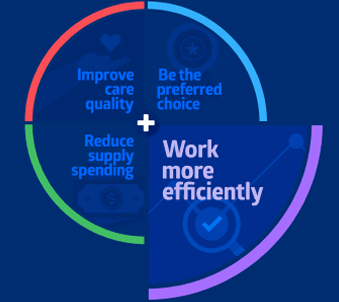
Organization
The City of New York
New York City comprises five boroughs sitting where the Hudson River meets the Atlantic Ocean. At its core is Manhattan, among the world’s major commercial, financial and cultural centers. New York City is also the most densely populated major city in the United States, with a 2020 population of 8,804,190 distributed over 300.46 square miles (778.2 km).
Challenges
- Find one warehouse location for all of NYC pandemic stockpile
- Give visibility and access to the inventory to NYC and its end users
- Integrate previously purchased supplies and all the city accounts into Medline’s e-commerce platform
Actions
- Outfit warehouse in record time to accept shipments of NYC inventory from various locations
- Bring all inventory into Medline’s existing SAP platform to manage and deliver all stockpile inventory
- E-commerce integration
Results
Work more efficiently:
- Medline’s sophisticated 3PL experience allowed for space and time optimization of the NYC stockpile inventory
- Integrating all the inventory into Medline’s enterprise and e-commerce platform allowed for a successful ordering and delivery platform
“We were looking for an organization to take over the coordination of logistics, warehousing, and inventory management, while having the right technology and a reliable transport operation for all the deliveries.”
Dan Symon
Chief procurement officer, NYC
Challenge
For perspective on how quickly everything went from feeling “normal” to anything but, only four days passed from the first public case of the novel coronavirus in NYC, a healthcare employee, on Sunday, March 1, to Friday, March 5, 2020, when NYC healthcare workers suddenly faced a shortage of N95 respirator masks. In a timeline of how the pandemic hit NYC in New York Magazine, this is the entry for Friday, March 5, from Michael Einhorn, president of Dealmed, a Brooklyn-based medical-supply company: “I’ve spoken to two hospital CEOs and one very high-ranking executive looking for N95 masks. Our call volume is up around 400 percent. We do have a very limited supply, but it’s only for our current customers. We take that decision very seriously. What’s more important, dialysis centers or a hospital? I’ve been through several of these cycles, none of those compare at all to the coronavirus.”1
Dan Symon, chief procurement officer for the NYC, was familiar with complex supply chain apparatus across the board—but even the most sophisticated healthcare supply chain teams in the city were struggling to get any PPE inventory whatsoever in the early days. For the city itself, medical supply is not typically a huge piece of their overall municipal procurement. Within days, it suddenly became a most critical component. As Symon recalls, they spent the first few weeks struggling, like everyone, to get whatever PPE they could and were stockpiling the inventory in a number of locations. By April, once they got their footing, they were able to start conceiving of a rational operation. It was clear the city needed to step in to provide a stockpile service center to support the entire healthcare center in NYC.
Meanwhile, in Chicago, Peter Saviola of Medline was also beginning to see the impact on the healthcare supply chain and how leaders and customers were beginning to react. By early-to-mid-March, Medline had been receiving calls for help managing stockpiles of inventory throughout the country. Medline had done this sort of thing in the past with third party logistics (3PL) and such, but the increased demand started streaming in from a variety of health systems and city and state municipalities. It was around late April, early May 2021, Saviola recalled, that the City of New York put out a request for proposal (RFP) for a professional operation and management of the stockpile program that would serve to back up the whole of New York City operations.
“It wasn’t just a physical logistics problem. There was a technology component needed to provide visibility and access to those supplies and then the management and replenishment of those supplies.”
Peter Saviola
Peter Saviola, VP supply chain, Medline
Medline’s warehouse of NYC pandemic stockpile
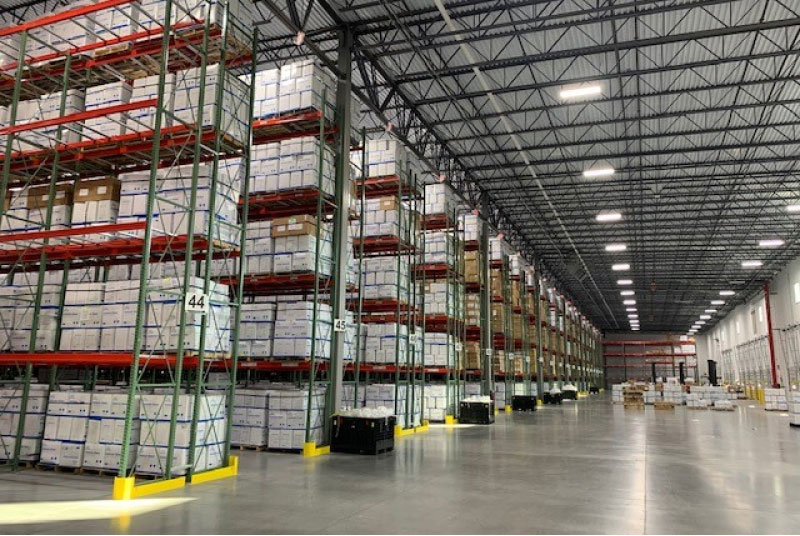
Actions
Once it became clear that Medline would handle the city’s stockpile program, the groundwork had already been set. An existing warehouse, nearby, had been selected to support the program. As Roger Polanco, director of supply chain, recounts, outfitting an empty warehouse typically takes anywhere from three to four months to rack it out and make sure all the labeling is correctly identified. When they took over this warehouse, less than 10% of the facility had any racking whatsoever, and it was clear that the incoming inventory would take up nearly half of the facility, and that shipments needed to start coming into the warehouse within weeks rather than months. Ultimately it took around six to eight weeks, as opposed to three to four months, with warehouse workers working around the clock (although given the height of COVID, protocols were strict in terms of how many people were actually able to be in the building at any one time—typically around 25-35 members). Rather than hiring people that they would have to let go once the job was complete, they brought in operation support team members from all over the country—Chicago, California, Florida—including people from New York. Luckily, they were able to focus on one customer, and with 70 doors in the building, the team was able to spread out and properly follow CDC guidelines throughout the outfitting of the warehouse.
“It was a very collaborative relationship from the very beginning. …we worked to build up the inventory, set up the users and ultimately implement the technology and distribution for the end user to procure the order.”
Brandon Reeder
VP operations, Medline
E-commerce integration
As the warehouse was being prepared, Medline’s digital team had been briefed on this distinct opportunity: prior to this project, there had never been any 3PL accounts brought onto Medline’s e-commerce platform. (As of the time this article was written, Medline has added two more such accounts, and they are working on a third.) As Kelley Molina, director of digital product management for medline.com, recalls, “None of this was our product, and they were all different case sizes and packaging. How do we display that on medline.com if we don’t know what is coming in the next shipments (for example if you have size medium gloves this week coming in a box of a hundred, but next week size and/or volumes are different)?” The biggest challenge was in figuring out how to represent products online, when the inventory being received was unexpected and had already been purchased. Luckily, the team was able to work with other Medline colleagues with expertise in SAP (Medline’s ERP software), handling and standardizing the inventory as it was received.
The first step was integrating everything on an enterprise level for all of the SKUs and then going from there. The other challenge, of course, was identifying all of the users. Medline created IDs for nearly 1300 unique accounts that would be able to place orders and established training for them on the ordering process. All of this needed to be done as quickly as possible, because without a platform to select and order the products, the larger goal of not only housing the inventory but getting it to the end user would not be possible.
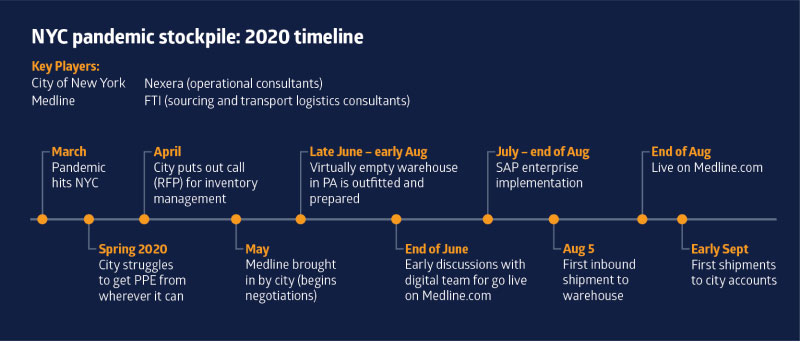
Supply chain in action
From the supply chain optimization side, teams were tasked with making sure that the distribution center was outfitted, the material handling equipment and systems were in place, so that when products started showing up in the building, Medline could receive everything quickly and put it into stock immediately. Typically, a project like this might require a year for everything to be up in running. As has been mentioned elsewhere, from late June to the launch date at the end of August/early September, the timeline was incredibly condensed to around two months. This is where Medline benefited from a solid infrastructure—from a core distribution network to logistical operations—that had been stress tested and could meet the unique demand. This inventory coming inbound to Medline wasn’t coming in from their own manufacturers or vendors, as usual. These goods had been previously acquired by the city, so everything was coming in different types of packaging that was unfamiliar and had varying units of measure for the same product—requiring different stacking or pallets than what Medline was typically accustomed. A turning point for the project was overcoming those obstacles, accounting for differences and communicating that back to the customers.
“We were coordinating inbound activity from a variety of places. …we had to make sure everything was coordinated and staffed appropriately so that we didn’t have too much product showing up at one time.”
Zach Malingowski
Supply chain optimization group, Medline
Scott Running, from Medline’s SAP team, realized from the start that this would be an ideal opportunity for Medline to help out New York City with their distribution of pandemic medical supplies. Scott and his team had developed expertise with how Medline manages orders for different customer groups like big box retailers, pharmaceutical companies, physician offices and individual customers. The NYC setup was complex as it required Medline to build an “inventory bubble” of customer owned and reserved non-valuated items. Scott managed the end-to-end process between customer, sales, operations, e-commerce and IS for set-ups and changes. The unique objective was that only New York City customers would be given access to view and order these specific items on Medline.com—a process more complex as most of these customers were existing Medline customers, but they had to be treated uniquely for ordering NYC pandemic Items. Medline’s experience with third party logistics allowed them the flexibility to pivot and come up with a solution to manage all aspects of the project—from materials, to customers, to technology adaptations in SAP, e-commerce and WMS.
“I would take a forward look and say, I hope we can use this as an object lesson on why business continuity planning needs to occur before the need arises. Because at that point, it’s often too late.”
Dan Young
Supply chain director, Medline
Results
In the end, when the NYC pandemic inventory program launched on Medline.com at the end of August 2020 and the first orders were delivered within 48 hours, all parties involved were relieved that at the end of the day they were able to execute exactly what they had conceived: all users were able to get on one single platform, create orders and know, with confidence, that they were being managed and delivered in a matter of one to two days, as opposed to the manual processes and longer delivery times that had been in place prior to this implementation. Not only that, but the city had visibility over the entire process, like never before. They could see what was coming in and approve it, but not have to manage anything else in the project. They needed a process that would get the goods from point A to point B in a small period of time, without a lot of user interaction.
NYC may have wanted one organization for the task, but ultimately it is always about the partnership and couldn’t have happened without the teamwork of everyone involved. As Dan Symon notes, it came down to the collaborative spirit of the players, even from the early days of the contract negotiation. “We squeezed six months into six weeks on a piece of work neither one of us had anticipated.” This partnership resulted in something special and unique during a critical time, and the results will have lasting effects: both for the city customers who depend on these supplies for some time to come and for Medline, who has been able to draw from this experience to meet similar demands for other customers.
1300+
Unique accounts set up on Medline.com for NYC
48 hrs
First orders upon launch delivered within 2 days
6 wks
6 months of work squeezed into 6 weeks