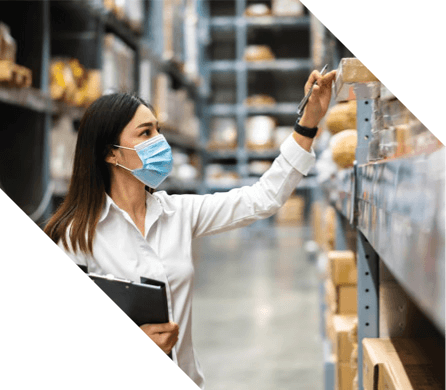
Insight
As we all know by now, the role of a healthy and robust supply chain is key to managing the disruption that comes from any major disaster. The toll taken from months and months of this pandemic has affected every level of the hospital system from administrator, to caregiver, to patient, with the manufacturers and suppliers struggling to get the right PPE and clinical products to the people who need them most. What has become more than transparent through the bulk of 2020 into 2021 is that the supply chain is only as healthy as the relationship between customer and supplier, with visibility into inventory needs and alignment on key planning strategies.
This case study showcases one of those partnerships between Medline and NorthShore University HealthSystem and outlines steps taken throughout the year to fight against shortages and disruption in what has been a most uncertain time.
Organization
NorthShore University HealthSystem
The NorthShore system, headquartered in Evanston, Ill., includes six hospitals—Evanston, Glenbrook, Highland Park, Northwest Community, Skokie and Swedish. NorthShore also includes a 900 physician multispecialty group practice, NorthShore Medical Group, with more than 160 locations in the Chicagoland area.
Challenges
- The need for PPE reinforcements at the beginning of the pandemic
- The growing demand for additional PPE storage
Actions
- 30 carts of PPE supplies delivered to Skokie Hospital in early April
- Support through warehouse design, racking quote and/or buildout, consulting, etc.
- Customized COVID kits for patients
Results
Work more efficiently:
- Using “U-boats,” the transfer from loading dock to guarded storage rooms happens in less than 20 minutes
- Increased domestic manufacturing for hand sanitizer and face masks
Challenges
In February 2020, Medline’s Newsroom posted an article “Preparing for Infectious Diseases in the Face of the Unknown,” where the question was posed: “How can healthcare providers prepare for emerging infectious diseases when practice and standards are yet to be set?” Dr. Kamal Singh, Director of Infection Prevention & Control at NorthShore University HealthSystem was direct in saying, “Successful planning involves the cooperation of all the members of a system. It’s not just infection prevention professionals. It also takes the nurses, doctors and other healthcare workers working in tandem.”1
The beginning of the pandemic in the US felt insurmountable, but Medline and NorthShore fell into step with one another, focusing on transparency and working together toward quick and efficient solutions. Early on in the pandemic, what NorthShore needed most was PPE reinforcements. By July, NorthShore found themselves needing more storage for their pandemic stock, and they reached out to their partner for help. They were quickly running out of room, and they required short term assistance (of around six months) as they were deciding on a long-term storage solution (leasing or buying their own warehouse). During the pandemic, Medline has responded to similar customer needs through 3PL (third party logistics) storage solutions in order to enable offsite, centralized storage and inventory transparency.
“Health systems are a lot better prepared to handle unknowns than they might have been in the past. For healthcare, infection control protocols aren’t just a one-dimensional solution. They’re a combination of infection control tactics that leads to success.”
Alan Weiss
ReadyCare division president at Medline

Actions
At the beginning of April 2020, with shutdowns in full swing and COVID-positive numbers rising, Medline was able to provide NorthShore’s COVID-19 patient care teams additional personal protective equipment (PPE). Thirty carts full of supplies—including gowns, gloves, N9Ss, isolation masks, thermometers and other PPE; the first delivery of many expected that month—were delivered April 2 to Skokie Hospital to be distributed throughout the system. “These are liquid gold on a cart,” said Carsten Gudella, Assistant Vice President, Corporate Supply Chain Operations.2
What is critical for the process is how to keep the supply distributions from interrupting the flow of any given day. Nicknamed “U-boats,” the supply carts are easily managed and moved by two individuals, avoiding the need for forklifts. All supplies are shrink-wrapped to protect them during transit and delivery. The transfer from loading dock to guarded storage rooms in a makeshift, onsite warehouse happens in less than 20 minutes. Once carefully inventoried, the supplies are shipped to system-wide hospitals, immediate care centers and drive-through test sites, among others. “The supplies are going out as fast as we get them in,” said Gudella.
During the summer, Medline’s MedTrans trucks initially backhauled 100 pallets of isolation gowns, hand sanitizer and masks to a Medline distribution center in Libertyville, IL, and the program has continued to grow from there. Since July 2020, at NorthShore’s request, Medline has periodically added excess product to the distribution center. Examples include backhauling product directly from Skokie Hospital, transferring bulk allocation purchases directly to 3PL storage (never leaving the distribution center), or coordinating a drop ship with vendors for direct delivery.
Discussing crisis preparedness and COVID-19, Medline had a brief conversation with NorthShore’s executive supply chain team to gather more insights on their operational infrastructure:
Q. Is supply chain management a strategic senior level position in your organization or is it a part of an operations activity?
A. NorthShore’s supply chain has long been a trusted partner for operations, and over the past five years have shifted to also being a strategic partner. The pandemic kept supply chain top of mind for many of our leaders and we have never felt more gratitude coming our way.
Q. Is your business model resilient enough to recover from the impact of a crisis and manage potential crises in the future?
A. If speaking specifically to COVID-19, then yes, we shifted the distribution model of our key supplies and PPE from LUM to bulk to have tighter inventory control and more flexibility during the pandemic and are building out a warehouse for supply chain pandemic stockpiles for the future. With respect to Clinical Operations at NorthShore, we have been incredibly nimble, adapting to the need of our community, standing up drive thru testing locations, pivoting Glenbrook Hospital into a COVID only hospital for a while, and shifting our entire care model.
Q. Do you have a built-in change management process that constantly reviews the elements of your supply chain and looks for opportunities to improve quality and operational efficiency—or do your systems, policies and procedures block improvement?
A. We do not have a built-in change management team focused on improving quality and operational efficiency, but our frontline managers and others are taught to always look for better ways to do our jobs so we can continue improving. Additionally, we partner closely with Medline to evaluate some of our key opportunities for improvement.
Q. Is Just-In-Time the right answer for your business in the midst of or aftermath of COVID-19?
A. Not for items impacted by COVID-19’s global supply chain disruption. As noted earlier, we are implementing a local warehouse and will always keep between 60-90 days of stock on critical items available in our possession locally. Eventually, we hope to be able to shift back to a full LUM/JIT program but at this point, it seems years away.
Custom COVID kits keep NorthShore top of mind
In the beginning of the pandemic, NorthShore realized that preventative guidance and the use of a pulse oximeter at home was key to managing their patients. NorthShore was determined to provide a free COVID Care Kit to symptomatic COVID positive patients who were not admitted. Medline worked with them seamlessly to implement the new kit and deliver over 16,000 kits to patients.
Results
By September 2020, NorthShore had plans to lease a warehouse in Glenview. They initially asked Medline for general warehouse consulting support. There were four distinct courses of action from Medline:
- Provide support through warehouse design, racking quote and/or buildout, consulting, etc.
- Store all product on a month-to-month lease
- Store all product with a long-term lease, with cheaper 3PL pricing
- Carve out a Consolidated Service Center
NorthShore ultimately decided on the first course of action, with Medline providing an initial warehouse design and associated racking quote for them in the event that they choose to go in that direction.
In addition to inventory and storage planning and other supply chain efficiencies, Medline has been actively working to increase domestic manufacturing for hand sanitizer and, most recently, face masks. In November, Medline announced plans to modify its Lithia springs, Ga. Plant and anticipates production to begin on Level-1 ear loop procedure masks in January. More than 30 healthcare providers spanning hospital systems, skilled nursing facilities and homecare providers, including NorthShore University HealthSystem, have already committed to purchasing the made-in-America face masks as part of Medline’s North American Manufacturing Expansion initiative.3
Executives and leaders throughout healthcare, from supplier to provider, understand now more than ever that in order to run a successful organization, a healthy, highly efficient supply chain is key. These days, staff and patients alike depend, quite literally, for their lives, on PPE, respiratory supplies and other products like needles and cold storage for vaccines. The quest, then, for a partnership that can work to execute solutions to avoid shortages, provide adequate storage and plan for the inevitable becomes an ever-important objective. What NorthShore and Medline have created through this pandemic is that sort of partnership. It may not be as valuable as “liquid gold,” but it’s pretty close.
References:
- https://newsroom.medline.com/infection-prevention/infectious-diseases-like-coronavirus-prep
- Strong supply chain bolsters patient care. Internal NorthShore newsletter.
- https://newsroom.medline.com/releases/medline-expands-manufacturing-in-north-america-to-meet-demand-for-face-masks