Insight
“We have to be prepared because the world is changing,” said Chris Toomes, UTMB vice president of supply chain. “One of the things that COVID-19 taught us, is the need to truly be prepared to protect our entire patient population, as well as the staff and faculty who are critical to patient care.”
Partners like University of Texas, Medical Branch (UTMB) are finding that inventory solutions like 3PL, a new customized third-party logistics stockpile management program provide them with the assurance they need by allowing them to take in large amounts of healthcare system-owned inventory and place it into Medline’s own distribution center infrastructure. The system is then able to utilize our systems, our technology and our logistics to provide visibility to those stockpiles.
What does this do for a system? Well, for one, it provides them the flexibility to divide their stock between multiple locations. As Toomes remarks, “We may have supplies on the island, but I need to take care of other locations. I use the 3PL program to extend the UTMB supply chain and direct the symphony, so to speak. I know what it is and where it is, and we can move it efficiently.”
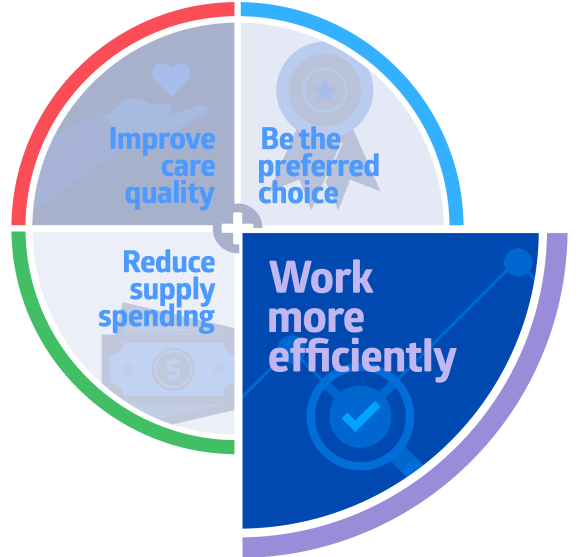
Organization
The University of Texas Medical Branch established in 1891 as the University of Texas Medical Department, has grown from one building, 23 students and 13 faculty members to a modern health science center with more than 70 major buildings, more than 2,500 students and more than 1,000 faculty. The UTMB system includes a medical school; schools of Nursing, Health Professions, and Public and Population Health; graduate biomedical sciences and research programs; four hospital campuses and more than 90 clinics throughout Southeast Texas.
Challenges
The transition from an older just-in-time, lowest unit of measure delivery system, to a system the takes shortages and emergency preparedness into account.
- Maintaining a sufficient stockpile of disaster inventory that meets the demand and is managed appropriately, taking into account expired, obsolete or damaged items.
- Most systems do not have the space to store new inventory.
Actions
UTMB utilizes data to more precisely analyze delivery and procurement patterns.
- The system regularly reviews surgical preference cards to reduce waste and supply duplication.
- UTMB has partnered with Medline to access more storage space and advanced logistics through 3PL and other solutions.
Results
The 3PL program is helping UTMB maintain a 90-day PPE stockpile.
Challenges
Like many healthcare systems, the University of Texas Medical Branch (UTMB) is prioritizing, diversifying and upgrading its supply chain processes and stockpiles to mitigate the effects of future crises and supply chain disruptions. The three UTMB hospitals located on the island of Galveston are especially vulnerable to severe storms and related supply chain instabilities.
Prior to the pandemic, most systems were moving to a just-in-time (JIT) delivery—or the lowest unit of measure—model. That made sense then; however, with shortages and other supply chain-related disruptions it is becoming more and more desirable to have a stockpile of PPE (personal protective equipment) and other critical items necessary to run a hospital.
In the years before 2020, most hospitals and healthcare systems had some disaster inventory; however, many stockpiles “were tremendously undersized, and there were not enough supplies to meet demand,” said Peter Saviola, Medline vice president, supply chain optimization. In addition, some stockpiles had not been appropriately managed over the years, resulting in supplies that were “expired, obsolete or damaged.” When supplies did become available for purchase, many healthcare systems did not have the space to store the new inventory.
Actions
Today, UTMB utilizes data to more precisely analyze delivery and procurement patterns, and regularly reviews surgical preference cards to reduce waste and supply duplication. In addition, the healthcare system has partnered with Medline to access more storage space and advanced logistics.
These and many other processes have been put in place as resiliency tools to help offset product shortages on the one hand and an overabundance of the wrong supplies, leading to waste and inefficiencies. It may not seem like it at first, but data is just as critical to maintaining a healthy stockpile solution as it is to operating and managing a streamlined JIT delivery system.
Results
To date, more than 70 healthcare systems are partnering with Medline through the 3PL program, which is supported by the company’s $2 billion, multi-year Healthcare Resilience Initiative (HRI). Since 2018, HRI has resulted in the construction of eight new distribution centers, including one near the Port of Savannah; nearly 150 manufacturing expansion projects; and a new global digital customer ordering platform. Medline has more than 20 manufacturing facilities in the U.S. In 2020, the company’s domestic manufacturing capabilities were expanded to include the production of 36 million face masks a month.
For UTMB specifically, the 3PL program with Medline is helping UTMB to maintain a 90-day PPE stockpile, providing reassurance that the health system can weather any crisis or storm.
For more information on 3PL and other inventory management solutions, read more about Medline’s approach to Supply Chain Optimization.